Introducing the Different Types of Light Weight Aluminum Spreading Processes for Precision Results
Aluminum casting procedures play a vital function in the production market, using a vast variety of strategies to achieve accuracy lead to the manufacturing of complex parts and parts. From die casting to sand spreading, investment spreading, permanent mold and mildew casting, and centrifugal spreading, each approach brings its own collection of advantages and details to the table. Comprehending the subtleties of these processes is essential for makers looking for to enhance their manufacturing processes and make sure the best end results. By exploring the unique features of each casting technique, a much deeper insight into the globe of light weight aluminum casting can be gotten, losing light on the optimal method for attaining precision lead to different applications.
Pass Away Casting Refine
The Pass Away Casting Refine is a very reliable production approach for generating geometrically intricate steel components with high accuracy and repeatability. This procedure entails compeling molten metal right into a steel mold and mildew dental caries under high stress. The mold and mildew, additionally referred to as a die, is commonly made in 2 components: the cover die half and the ejector die half. These dies are developed to create the desired shape of the end product.
One of the essential advantages of die spreading is its capability to produce parts with slim walls, elaborate information, and smooth surface areas. This makes it a favored choice for sectors such as vehicle, aerospace, and electronics where intricate steel components are called for. Furthermore, die casting deals exceptional dimensional accuracy, enabling very little post-processing requirements.
Moreover, die spreading can be categorized right into hot chamber and cool chamber die casting processes. In warm chamber pass away casting, the molten steel is contained in a heater while in cold chamber pass away casting, the liquified metal is ladled right into the cold chamber for every shot. aluminum casting. Each method has its very own collection of advantages and is picked based on the details requirements of the task
Sand Casting Technique
Utilizing a centuries-old method, the sand spreading method is an extensively used procedure in the production industry for developing steel elements. This approach involves producing a mold and mildew made of compacted sand right into which molten metal is put, permitting it to take the form and solidify of the mold tooth cavity. Sand spreading is valued for its flexibility, as it can generate a wide variety of intricate sizes and shapes, making it appropriate for different sectors such as auto, aerospace, and art factories.
Among the essential benefits of sand casting is its cost-effectiveness, especially for low to tool volume manufacturing runs. Additionally, the sand mold and mildews can be reused several times, minimizing material waste and overall manufacturing prices. Despite its long history, modern-day improvements in sand spreading strategies, such as using computer simulations for mold design and 3D printing for producing complex patterns, have actually better boosted the precision and performance of the procedure. Overall, the sand spreading approach continues to be a popular choice for manufacturers seeking a economical and reputable method to produce premium metal parts.
Investment Casting Technique
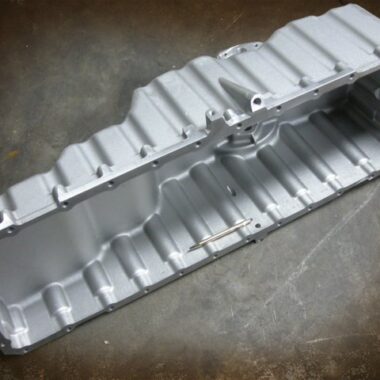
This technique is preferred for its capability to create complex forms with high accuracy and great surface area finishes. Industries such as aerospace, automotive, and precious jewelry depend on investment spreading for elements that require limited tolerances and detailed information. The process allows for cost-efficient production of tiny to medium-sized parts in various products, making it a versatile option for producers looking for precision outcomes.
Permanent Mold And Mildew Casting
With an emphasis on creating steel components with a reusable mold and mildew, Permanent Mold and mildew Spreading provides a different method to the intricate precision of financial investment casting. aluminum casting. This technique, also understood as gravity pass away casting, includes the usage of a long-term metal mold and mildew generally made from steel or cast iron. The mold and mildew is preheated prior to the liquified metal is poured right into it, allowing for faster solidification compared to sand spreading
Permanent Mold Casting makes it possible for the production of top notch, dimensionally exact get rid of a fine surface area coating. By utilizing a recyclable mold and mildew, manufacturers can achieve expense financial savings over time as the mold can be utilized several times without substantial wear and tear. This process is optimal for high-volume manufacturing runs where uniformity and performance are essential.
One of the crucial benefits of Irreversible Mold and mildew Spreading is its ability to produce web complex shapes and elaborate styles effortlessly. aluminum casting. The approach is extensively made use of in the auto, aerospace, and electronic devices sectors for manufacturing components such as engine parts, heat sinks, and architectural components

Centrifugal Spreading Method
The Centrifugal Spreading Technique is a method that entails rotating a mold and mildew at broadband while putting molten metal right into it. This process makes use of centrifugal force to disperse the molten metal equally along the walls of the mold and mildew, leading to a high-quality, thick spreading. The centrifugal force presses impurities and gases towards the internal diameter of the casting, bring about a cleaner final product with boosted mechanical residential properties.
One of the essential benefits of centrifugal casting is the capability to generate cylindrical or disk-shaped components with a fine-grained framework that enhances the mechanical residential properties of the spreading. This method is especially ideal for developing symmetrical parts such as tubes, pipelines, and rings. In addition, centrifugal spreading provides the advantage of being a cost-effective procedure with relatively low tooling expenses compared to other casting techniques.
Verdict
In verdict, understanding the different sorts of light weight aluminum spreading processes is essential for accomplishing exact lead to production. Each approach has its very own benefits and constraints, making it vital to select the most suitable procedure based upon the details needs of the project. visit the website Whether it is pass away spreading, sand spreading, financial investment spreading, long-term mold casting, or centrifugal casting, choosing the right technique can lead to top quality and affordable production outcomes.
From die spreading to sand spreading, investment casting, permanent mold and mildew site here spreading, and centrifugal casting, each method brings its very own collection of advantages and complexities to the table. By discovering the unique qualities of each casting approach, a much deeper insight right into the globe of aluminum spreading can be gotten, dropping light on the optimal strategy for accomplishing precision outcomes in different applications.
In hot chamber pass away casting, the liquified metal is contained in a heater while in chilly chamber die spreading, the molten steel is ladled into the cool chamber for each shot.With a focus on creating steel components via a reusable mold and mildew, Long-term Mold Casting offers a different method to the detailed precision of financial investment casting. Whether it is pass away casting, sand spreading, investment spreading, permanent mold spreading, or centrifugal casting, picking the right strategy can lead to affordable and high-quality production end results.